As a young student architect, Arthur O’Brien remembers helping design classic McDonald’s restaurants.
A revolutionary build at the time, the iconic franchises were modular buildings, where the majority of the structure was built in sections in a factory and then assembled on site in a fraction of the time of the traditional bottom to top building style.
“Our race was to see how quickly after we move on site can we deliver the first burger,” he said. “I think we got it down to 15 days, a tremendous achievement back then.”
O’Brien has since graduated from designing small fast-food restaurants and is now managing director of C+W O’Brien Architects, one of Ireland’s largest designer of modular buildings.
Companies like C+W can have multi-storey high-rises assembled in the same timeframe it took to build O’Brien’s McDonald’s designs decades ago, and the unprecedented speed and efficiency left many hailing modular buildings as the solution to Ireland’s housing crisis.
In the past 18 months, though, the modular housing sector in Ireland has seen massive setbacks, due in large part to added strain on the private housing market and a shortage in construction supplies caused by the pandemic.
“The big problem at the moment is that we cannot meet the demand, our supplies are so short,” said Alex Pankoff, CEO of Nühaus, a Dublin-based modular building company that works exclusively in the residential home market.
“We have a huge amount of enquiries and requests, but our hands are tied, we just can’t deliver.”
The cost of a pandemic
The price of construction timber in Ireland has risen by 5 per cent in the last 12 months, according to Linesight, a professional services company that works exclusively with the construction industry.
The reason, like most momentous economic changes in the past year, is the pandemic. From cutting down trees to building the infrastructure necessary to transport timber, all forestry operations must first be licensed by the Department of Agriculture. When the pandemic struck, the department briefly stopped issuing these permits – a process already slowed down by objections from activists opposed to current forestry policy – which created a nationwide timber supply backlog. This lack of supply, coupled with the recent surge in demand for construction projects thanks to lifted restrictions, has caused a scarcity of timber in Ireland.
Europe is also dealing with a steel shortage due to similar causes of stunted mill production during the pandemic, which altogether has put an unprecedented strain on the Irish construction market.
The shortage has even caused one Irish company to pull out of the modular housing industry altogether.
Skyclad, a Westmeath business that primarily sells industrial steel roofing and walls made for agricultural buildings, had a modular housing subsidiary that the company shut down in the past month.
“Overnight, everything came to a standstill,” said Shauna Coyne, COO of Skyclad.
“We found it extremely difficult to get raw materials, and most people came to a stage where they either can’t afford [to buy a house], or they decided not to because of the circumstances.”
Coyne explained that the supply shortage impedes modular builders more than traditional builders since modular building requires virtually all of the necessary materials for the entire structure present at the factory at once to build quickly and efficiently. Traditional builders, on the other hand, may be able to build with what they have until more supplies arrive.
Skyclad has now almost entirely shifted to its industrial construction speciality, but even that market has struggled due to the shortage in steel, Coyne said.
The knock-on effect on social housing
Skyclad’s departure from the modular housing sector means one less company able to deliver fast and reliable social housing, a harsh blow to the effort to solve the housing crisis, according to Eibhlin O’Connor, head of new business at Clúid Housing, a non-profit organisation that helps provide homes to people in need.
“I think modular housing is the solution to the housing crisis,” O’Connor said. “It’s much faster, more efficient, and more lean.”
Clúid serves as the middleman between local authorities and construction companies. Local authorities across the country identify people and families who need housing, and where best to locate that housing. Then, Clúid raises the money to pay private construction companies to build the properties.
Clúid now houses over 21,000 residents across 8,000 homes, and with 3,000 more scheduled by the end of 2022, the organisation is integrating an increasing amount of modular housing into its portfolio, O’Connor said.
“Modular gives us much better control over quality and finish, there is no block laying or bricklaying, and we are not reliant on labour or trades which are usually segmented and inconsistent,” she said. “The whole thing is built in one place by the same people in a controlled environment.”
O’Connor also said that modular homes are much better value for money.
“It’s not necessarily cheaper [to build modular], but we do expect it to be faster and of a higher quality and consistency.”
All modular building falls into one of two categories, 2D and 3D, O’Connor explained.
2D construction means sections of the building are made in the factory, such as a wall attached to a ceiling, and then shipped to the building site where they are assembled together. 3D construction is when an entire unit, such as a house or apartment, is constructed in a factory and then placed into its foundation in one step.
2D modular construction makes up the vast majority of Ireland’s modular market, especially in social housing, as building authorities like Dublin City Council prefer the style, O’Connor said.
Declan Murtagh, CEO of modular building company Framespace Solutions, agreed with O’Connor’s take on the effectiveness of the modular style in social housing.
“Modular housing works really well with repeatability; It’s a standardized system,” he said. “If you’re building a once-off house in the country, they are all bespoke, people have little preferences and things they want. Social housing is standard and consistent. The materials and design are exactly the same, so it turns into an assembly line in the factory.”
Framespace works mostly in the private residential market, building modular homes for single customers, but the company has two active social housing projects they are working on with Clúid.
Murtagh said that speed and standardisation not only make for a consistently higher quality product across the board but it also allows for more housing to hit the market sooner, satisfying more people’s housing needs.
Modular building isn’t the first new-age solution for the housing crisis Ireland has seen, though.
A printed house?
In 2018, founders of 3D printing company Mcor Technologies, brothers Conor and Fintan McCormack, made headlines claiming that they could solve the housing crisis by 3D-printing homes.
Mcor had first gained traction in the early 2000s by developing a new 3D paper printing technology able to glue several layers of paper together, colour them with immense precision, and trim edges to create intricate paper sculptures.
With the right resources and infrastructure, Conor McCormack said that Mcor could scale the technology to 3D print homes faster and for less money than modular building.
The idea, along with the company, came crashing down in 2019, though, when Mcor went into liquidation.
Deloitte headed up the task, citing the inability to secure investments to pay for growth and expansion as the reason for the company’s demise.
Despite their innovative ideas, Mcor failed due to their inability to create a sustainable business model from the ground up. For modular building companies, this has proved challenging during the pandemic.
Even with the social housing projects available to companies like Framespace, modular housing businesses still must occupy the majority of their work with private clients.
The payment problem
This section of the market has been a struggle for many companies during the pandemic due to the unorthodox way customers pay for modular housing.
Because modular homes are first built in a factory and then later assembled on site after most of the labour is complete, purchasing one often requires a down payment of over 85 per cent, according to Alex Pankoff of Nühaus.
“These days a reasonable person might not be able to afford to build because of the prices,” Pankoff said. “The virus has put a lot of people in a position where they might not have the capital to pay for most of a house upfront.”
Nühaus builds its homes in factories located in Lithuania and Germany, and then ships them to Ireland.
Pankoff said that despite the financial constraints many prospective homeowners are under, his company still isn’t struggling with demand thanks to the backlog of projects that were paid for and ready to launch before the pandemic hit, and were delayed.
Where the pandemic has done a great deal of good for modular building in Ireland, though, is in the commercial sector.
With healthcare a significant client for many modular building companies, several responded to the health crisis by building isolation pods, emergency treatment centres, and even large-scale hospital extensions.
“We built private isolation units for people who couldn’t isolate in their own homes, usually because they lived in a crowded home,” Skyclad’s Coyne said. “We also built pods for members of the Travelling Community that couldn’t properly isolate.”
Both projects were funded under social housing, where local authorities would identify community members who needed the pods and pay Skyclad for the construction.
CPAC Modular, a company that makes modular buildings for the education, pharmaceutical, and corporate markets, took on the even more enormous feat of building space for extra hospital beds and other emergency healthcare infrastructure.
During the height of the pandemic, CPAC worked with St Vincent’s hospital in Dublin to rapidly build pods for additional treatment beds, as well as examination areas and administrative offices for the overflow of staff required to handle the surge in patients.
“We had already been building bed space for hospitals going back a few years, and when it became a huge need in Ireland to get a lot more very quickly, there was no learning curve for us, it was business as usual,” said Ciaran Flanagan, marketing director of CPAC Modular.
ESS Modular, another modular building company focused solely on the commercial sector, just built a permanent 72-bed ward extension to St Luke’s hospital in Kilkenny in 30 days in response to the nationwide demand for increased hospital space. The building is in the outfitting stage and is expected to open in October, according to ESS managing director Ronan Smyth.
At the end of 2019, the company was responsible for building Ireland’s largest modular healthcare project to date, a timely 40 room ICU addition to South Tipperary General Hospital that saw exhaustive use during the pandemic.
A commercial opportunity
The commercial modular building sector has seen success beyond healthcare in the past year as well.
“We’ve seen a very strong sales drive and demand with our projects over the last 2-3 months,” CPAC’s Flanagan said.
The company recently completed an extension to Dublin’s Griffeen Community College and is responsible for building the terminals at Dublin Port.
“The Covid period has put pressure on permanent projects, and it has shown how vulnerable traditional construction can be to influence from outside forces,” Flanagan said.
Many commercial modular building projects continued straight through the pandemic at the factory stage as government restrictions could be better enforced in a controlled factory environment rather than a construction site, Flanagan explained. This led to traditional construction projects falling far behind modular projects.
“It has allowed the market to look at modular as a solution where they haven’t before. Modular has come far enough where there are living examples [customers] have been able to look at and say ‘wow, that really works’. It really does surpass any expectation architecturally and style-wise.”
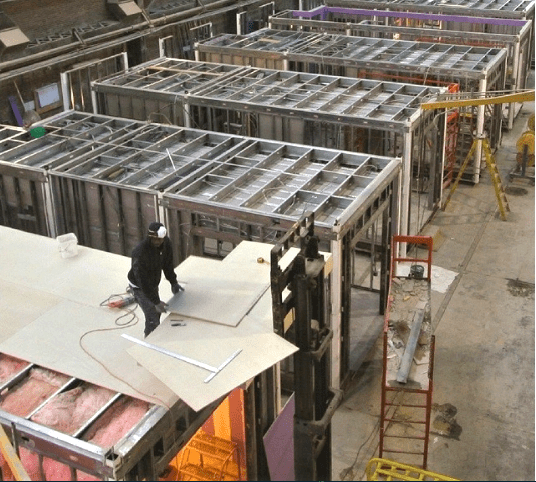
At the residential level, prospective homeowners have had a more open mind about modular building as well, according to Nühaus’ Pankoff.
“In general, we have no problem at all with people’s willingness to give it a shot,” he said. “20 years ago, this kind of thing had a wow factor, and people were a bit afraid, but today we’ve found that people are accepting and receptive to the benefits.”
Construction engineers, on the other hand, haven’t had the same change of heart.
“Engineers are old-school, old-fashioned guys. They don’t want to accept new foundations or new pre-built homes,” Pankoff said. “They like steel beams and bricks. This is just something new for them to accept, give it another 10 years and that will change.”
An aspect that has helped the popularity of modular building in the eyes of professionals is its nearly identical regulatory process compared to traditional building.
In fact, the modular regulatory process is much quicker. During the construction of any structure, inspectors visit the site at various prescheduled stages of the building process, according to Ronan O’Brien, Construction Industry Federation (CIF) executive.
That system is the same for modular building, except instead of an inspection taking place five or ten times throughout construction, it takes place once or twice depending on the size of the project.
“For really large-scale projects we may send an inspector over twice, once in the middle and once at the end, but for most modular construction it’s the same process with just one inspection,” CIF’s O’Brien said.
The attention that modular building has garnered over the pandemic has illustrated one downside of the modular process, though: it is not very agile.
“You have to buy into the whole modular journey very early on,” said Framespace’s Murtagh. “With the holdup of traditional construction, we have gotten interest from a lot of people who are halfway through a project and want to accelerate and go modular. It can’t really work like that, the process has to be set in stone from the very beginning.”
C+W’s O’Brien said the front-heavy process puts tremendous pressure on both the architects and the customers at the project’s early stage.
“You have to make pretty much all of your decisions in the first quarter of the project,” O’Brien said. “This is everything from the design itself to details like the finish and the windows. The time to change shrinks very quickly, and this can be problematic for some people.”
What customers sacrifice in flexibility, though, they make up in efficiency, safety, and environmental friendliness.
“One of the benefits of modular construction is that it’s easy to sort out any issues with the build once it’s complete,” O’Brien said. “You’re not trying to fix a pane of glass on the 20th floor in the middle of a city. You can fix it on the ground floor of a factory.
Safe and environmentally friendly
Modular construction is also a much safer alternative to traditional construction.
“Building on site has lots of safety risks, people walking around under machines, loose materials, blades, high structures,” CPAC’s Flanagan said. “In the factory setting you get very little of that, and it is even more safe for workers and people to move around the building site [after the factory stage]. Everything is just craned in position. There is not much hands-on required from workers, which means much less risk for the workers and the people around the building site.”
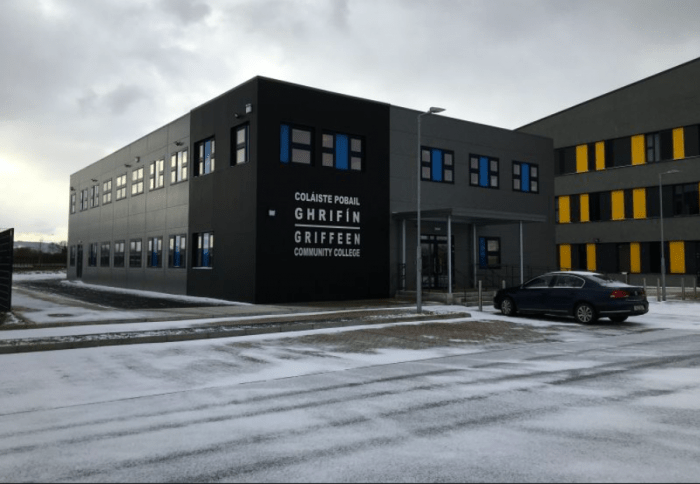
The streamlined building process also means less waste and a smaller environmental footprint.
“The benefit of standardization is that we can reuse the same steel profile and the same batch of materials, all ordered to the factory in the exact quantity we need,” said Framespace’s Murtagh. “We are not getting piecemeal deliveries of supplies, which is usually very fragmented and ends up with lots of material left on the cutting room floor.”
Many builders are hopeful for modular building’s future in the commercial sector thanks to its efficient and holistic approach to construction. They are less optimistic, however, about its future in the residential market.
“Only large projects are really suitable for modular development,” said C+W’s O’Brien. ‘Any scheme below 200 units really wouldn’t be suitable profit-wise. How many apartment buildings or social housing projects have more than 200 units, maybe some, but compare that to how many large data centres or pharmaceutical facilities that need more than 200 units and it’s clear where the work is worth doing. That sets the bar right there.”
O’Brien added that commercial projects also have a more lucrative price point.
“Student housing will have a value of x, apartments will have a value of 2x, hotels, also 2x, but pharmaceuticals and data centres will have a value of 10-100x depending on their complexity,” he said.
CPAC’s Flanagan agreed with O’Brien’s stance.
“Modular really is the future for building, especially for schools and healthcare,” he said. “These are institutions that usually need big projects turned around very quickly and that are built to last, and that’s what modular offers.”
For Ireland’s modular evolution to take its next step, it needs to get more building factories onshore instead of importing homes from the rest of Europe, O’Brien said, but that can only happen if there is enough demand.
“Once you build a factory, you have to keep building those buildings inside,” he said. “You can’t stop building or else the factory stops, so we need a big feed of work to make that happen. That’s why most modular factories are from outside the country, because they can support the demand of all of Europe at once.”
C+W is one of the few companies that work with plants in Ireland, sourcing from manufacturers located in Limerick, Galway, Cavan, and Monaghan.
That wide-scale Irish demand likely won’t come anytime soon, O’Brien said.
“Modular will only ever occupy about 5-10 per cent of the whole construction market, but it will occupy the top end of the construction market,” he said. “Modular is where all the big players will end up in the end, right now, they are all in the elite 5-10 per cent.”